GRUNDORAM The dynamic ramming technique
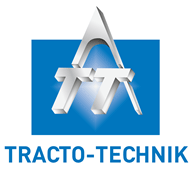
The steel pipe ramming technique is suitable for installing longitudinally or spirally welded pipes, seamless pipes and pipes with insulation protection as product pipes, e.g. in pipeline construction, or as casing pipes for supply und drainage pipe bundles. The pipe rammers are also used horizontally for constructing underpassees, small outlets, pipe roofs for tunnel structures, for supporting HDD bores (HDD Assist). Vertical applications are foundations, sheet piling or well drilling.
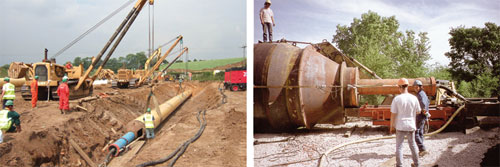
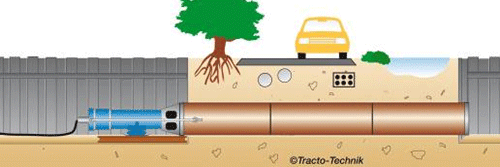
GRUNDORAM technology
The air driven piston inside the machine body strikes against the ramming head. The cinetical impact energy which is released that way enables maximum advancing of the pipe string due the the optimal force transmisision via the cones. As the constant loads affecting the machine require maximum product quality, the one-piece casing (head and casing are one part) is made out of a solid block which is thoroughly galvinzed. The piston is subject to an elaborate hardening process. A tight sealing minimises air consumption. Thus GRUNDORAM stands for durability and reliability.13 powerful models
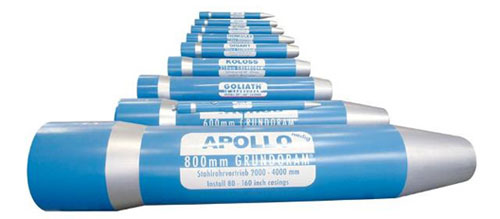
Only 3 main components
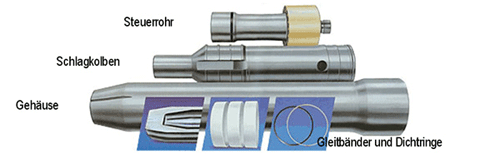
Installations lenghts / Pipe diamters / Machine types
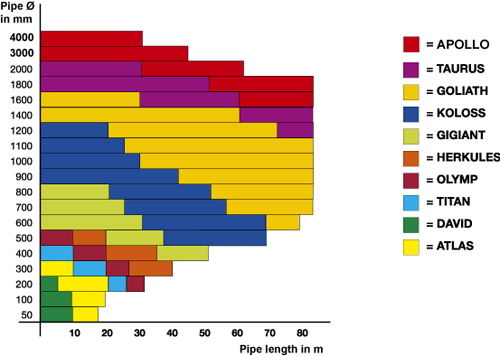
GRUNDORAM Accessories
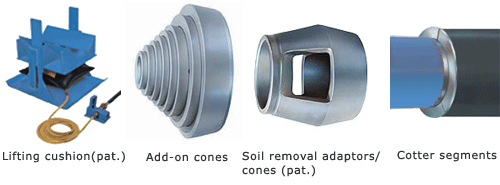
-
Lifting cushion(pat.)
enables exact and simple alignment of the ramming machine behind the steel pipe -
Add-on cones
guarantee a tight-fitting, stable connection between pipe and ramming machine. -
Soil removal adaptors / cones (pat.)
ensure a stable connection between pipe and ramming machine thus -
Cotter segments
enable the production of a butt welding seam, because the pipe is not flared when ramming, thus detachment at the
Leistungsdaten
GRUNDORAM Type |
Maschine Ø (mm) | Ø rear cone(mm) |
Length (mm) | Installation i Pipe (mm) |
Weight (kg) | Air consumption (m³/min) |
No. of strokes (min-1) |
Impact energy (Nm) |
From Pipe DN |
---|---|---|---|---|---|---|---|---|---|
David | 95 | 112 | 1490 | - | 59 | 1,2 | 345 | 230 | 50 |
Atlas | 130 | 145 | 1453 | - | 95 | 2,7 | 320 | 420 | 50 |
Titan | 145 | 160 | 1545 | - | 137 | 4,0 | 310 | 800 | 100 |
Olymp | 180 | 195 | 1690 | - | 230 | 4,5 | 280 | 890 | 100 |
Herkules | 216 | 235 | 1913 | - | 368 | 6,5 | 340 | 1440 | 120 |
Gigant | 270 | 300 | 2010 | - | 615 | 12,0 | 310 | 2860 | 200 |
Koloss | 350 | 400 | 2341 | - | 1180 | 20,0 | 220 | 6820 | 280 |
Goliath | 460 | 510 | 2852 | - | 2465 | 35,0 | 180 | 11600 | 380 |
Taurus | 600 | 670 | 3645 | - | 4800 | 50,0 | 180 | 11600 | 380 |
Apollo | 800 | 900 | 4400 | - | 11500 | 100 | 180 | 40500 | 600 |
Mini-Atlas | 125 | 140 | 946 | 250 | 60 | 1,7 | 580 | 180 | 50 |
Mini-Olymp | 180 | 230 | 1080 | 450 | 175 | 3,5 | 500 | 720 | 100 |
Mini-Gigant | 270 | 330 | 1230 | 450 | 460 | 10,0 | 430 | 2000 | 200 |
Advantages of the technique:
- less disruption and damage of surfaces worth conserving (road surface, front gardens etc.) and minimal restoration – giving economic advantages
- low social costs because detours, half-sided barriers, traffic signal facilities etc. are avoided
- acknowlegded pipe installation technique
- short setting-up times - short installation times
- the dynamic impact when ramming can shatter obstacles and easily overcome difficult starting resistance after standstill periods. The aiming accuracy is improved because the dynamic impact shatters various soil formations within the diameter range and obstacles don’t have to be displaced or pushed aside in one piece
- no jacking abutment, no auger cutter required, which could get jammed
- the soil core remains in the pipe during ramming, i. e. no inrush of water when rivers or high water table areas are undercrossed
- minimal covering, i. e. no large-scale pits
- simple operating technique
- adaptation to all pipe diameters with special ram cones
- wide application range